News
"Problem Solving: guardare la sicurezza con gli occhiali 8D"
fonte www.puntosicuro.it / Formazione ed informazione
06/02/2014 -
Un nostro lettore descrive esperienze pratiche per migliorare
l’efficacia degli interventi di prevenzione e gestione dei rischi nelle
aziende. E lo fa proponendo attività di “problem solving”,
un
processo messo in atto per analizzare un problema e trovare una soluzione.
La “ Metodologia delle Otto Discipline” è un’esperienza straordinaria di Problem Solving, orientata al lavoro di gruppo.
La “ Metodologia delle Otto Discipline” è un’esperienza straordinaria di Problem Solving, orientata al lavoro di gruppo.
Concepita alla fine degli anni 80’ dal Management della
Ford Motor Company, si pone l’arduo
compito d’individuare, correggere ed eliminare i problemi ricorrenti
nell’ottica del miglioramento
continuo del prodotto e dei processi aziendali.
Sarà possibile applicarla alla Salute e alla Sicurezza sul
Luogo di Lavoro, magari, per l’ analisi
degli incidenti, degli infortuni o dei near
miss? La risposta è: “Certo che si”. Aiuterò il lettore, attraverso un
esempio pratico, a utilizzare correttamente la metodologia. Buona visione!
D0 - Preparare e
Creare Consapevolezza
Datori di Lavoro, RSPP, ASPP, Preposti, CSE, CSP, Direttori
dei Lavori, RLS, Medici
Competenti, siete tutti comodamente seduti sul divano? Bene, il film può
cominciare!
È essenziale innanzitutto prepararsi per l’8D. Un certo
livello d’istruzione e formazione è necessario prima che il metodo 8D funzioni
efficacemente in un'organizzazione. Sul World Wide Web sono a disposizione
innumerevoli fonti. Basta cliccare sul più comune motore di ricerca Google e
digitare: “
Problem Solving”, “
Metodologia 8D”, per vedersi
catapultati, senza neanche accorgersene, nel mondo fantastico delle otto
dimensioni!
D0
Un operario, in seguito ad una movimentazione
manuale di un pannello di vetro, nella sala ispezioni, ha riportato un
taglio nel pantalone provocandosi una lieve ferita.
L’obiettivo è di analizzare l’evento attraverso l’8D Problem
Solving. |
D1 - Stabilire il
Team
Prepari un team interdisciplinare (con un team leader
efficace) che ha la conoscenza, il tempo, l'autorità e l'abilità per risolvere
il problema e implementare le azioni correttive. Regoli la struttura, gli
obiettivi, i ruoli, le procedure e i rapporti per stabilire un team efficace.
Perché la necessità di un team? Non conoscete quell’antico
proverbio orientale: “L’unione fa la forza!”. Molti scienziati e studiosi sono
arrivati alla risoluzione di un complesso teorema matematico: 1 + 1 = fa più di
2.
Lavorare in gruppo crea valore aggiunto e ne abbiamo le
prove ma attenzione, la ricerca dei componenti del gruppo deve avvenire con
criterio.
D1
Caso 1
Team Leader: RSPP
Gruppo Interdisciplinare: Lavoratore Coinvolto,
Responsabile della Sala Ispezioni, Dirigente per la Sicurezza
Caso 2
Team Leader: Responsabile Vendite
Gruppo Interdisciplinare: Operatore di Logistica,
Segretaria, Preposto Ditta Esterna
Quale fa al “Caso” nostro? |
D2 - Descrivere il
Problema
Definire il problema nei termini misurabili. Specificare
il problema del cliente interno o esterno descrivendolo nei termini specifici e
quantificabili.
Gli appassionati di serie poliziesche sono avvantaggiati
per portare a termine questa fase! Avete necessità di descrivere il problema,
in modo lineare con chiarezza e oggettività. Vi consiglio l’analisi 5W2H che
tradotta in italiano significa chiedersi:
D2
1
) Chi? 2) Che
Cosa? 3) Quando? 4) Dove?
5) Perché? 6) Come? 7) Quanto?
1) operatore 2)
taglio pantaloni 3) 23 dicembre
2013 4) sala ispezioni 5) l’angolo del pannello non integro 6) durante rotazione manuale vetro 7) nessun costo.
Elementare, Watson! L’obiettivo non è trovare il
colpevole, bensì, la soluzione affinchè l’evento non possa verificarsi
nuovamente in futuro. |
D3 - Implementare e
Verificare le Azioni di Contenimento Intermedie
Difficoltà provvisorie. Definire e implementare quelle
azioni intermedie che proteggeranno tutti i clienti dal problema fino a
implementare l'azione correttiva permanente. Verificare l'efficacia delle
azioni di contenimento con i dati.
Dal vocabolario Treccani la parola “
contenere” può essere definita come: frenare, anche con riferimento
alla resistenza difensiva in battaglia.
Il team leader e i suoi soldati hanno il dovere di
contenere e frenare i danni potenziali derivanti dall’evento accaduto, in
attesa, che sia perfezionata la strategia per vincere la guerra e liberare
l’azienda dalla non sicurezza sul luogo di lavoro.
D3
L’RSPP ha disposto che in attesa del completamento
dell’analisi 8D non sarà più possibile movimentare vetri in sala ispezione. |
D4 - Identificare e
Verificare le Cause alla Radice
Identificare tutte le cause potenziali che potrebbero
spiegare perché il problema è accaduto.
Diagramma
Causa Effetto. Verificare ogni causa potenziale con la descrizione e
i dati del problema. Identificare le azioni correttive alternative per
eliminare la causa alla radice. Si noti che esistono due tipi paralleli di
cause alla radice: una Causa alla Radice dell'Evento (il sistema che ha
permesso il verificarsi dell'evento) e una Causa alla Radice della Fuga/Punto
di Fuga (il sistema che ha permesso la fuga, senza rilevazione, dell'evento).
Propongo
3
possibili menù per l’identificazione della causa:
- Menù di pesce: “Diagramma di Ishikawa”;
- Menù vegetariano: “Albero di guasto”;
- Menù bambini: “5 Why”.
Il
Diagramma di
Ishikawa, conosciuto anche come diagramma a lisca di pesce, consiste in una
tecnica grafica utilizzata dal team per organizzare tutte le idee che possono
essere correlate alla causa potenziale del problema.
L’
albero di guasto
può essere utilizzato, se ancora non si è sazi, per analizzare in modo
deduttivo il sistema e le sue performance connettendo all’evento incidentale,
attraverso i simboli logici “and”, “or”, gli errori critici.
Il
5 Why, è un
metodo utilizzato ogni giorno inconsciamente da tutti i bambini del mondo.
Illustrare la catena causa-effetto connessa al problema domandansi per 5 volte:
Perchè?
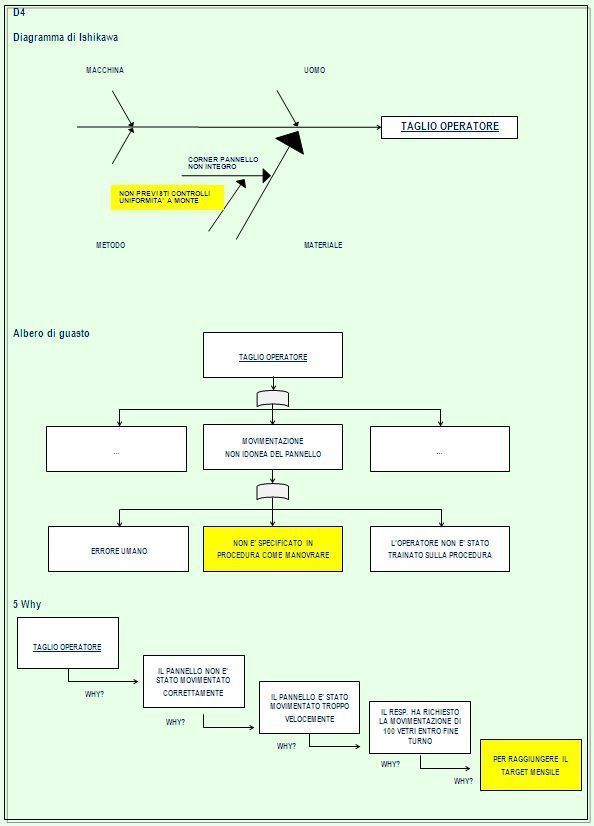
D5 - Scegliere e
Verificare le Azioni Correttive
Confermare che le azioni correttive selezionate
risolveranno il problema per il cliente e non causeranno effetti secondari
indesiderati. Definire le azioni di contingenza, se necessario, basate sulla
severità potenziale degli effetti secondari.
D6 - Implementare e
Convalidare le Azioni Correttive Permanenti
Scegliere i comandi continui per assicurare che le cause
sono state eliminate alla radice. Almeno una volta nella produzione,
controllare gli effetti di lungo termine e implementare comandi e azioni di
contingenza supplementari secondo i bisogni.
D7 - Impedire la
Ricorrenza (Prevenzione)
Identificare e implementare le fasi che devono essere
intraprese per impedire che si verifichi di nuovo lo stesso problema o un
problema simile nel futuro: modificare le specifiche, aggiornare la formazione,
rivedere il flusso lavorativo e migliorare i sistemi di gestione, i sistemi
operativi, le pratiche e le procedure.
Per portare a termine le fasi D5-D6-D7 è necessario
stampare in mente, a colori, e ad altissima risoluzione, il “
Ciclo di Deming”. Il genio di Edwards
Deming ha insegnato come si può aumentare la qualità e contemporaneamente
ridurre i costi. La chiave è quella di praticare un continuo miglioramento.
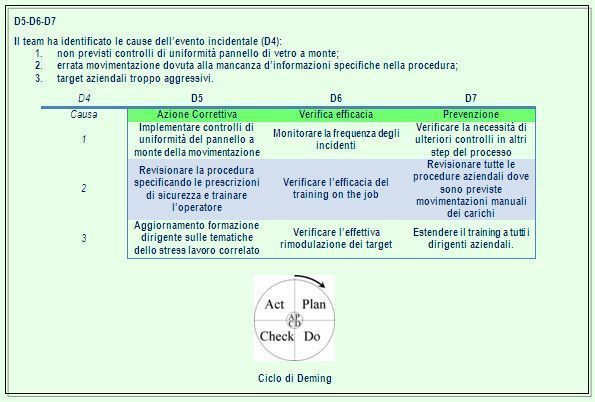
D8 - Congratularsi
con il Team
Il team leader deve riconoscere e gratificare gli sforzi
profusi dal team. Il successo dell’esperienza dovrebbe essere trasmessa a tutta
l’organizzazione aziendale e capitalizzata in un LLC (
Lesson Learned Chart).
D8
Un ringraziamento è dovuto anche a chi ha preparato e
condiviso queste informazioni, non pensate!
THE END |
Sebastiano Trapani
Segnala questa news ad un amico
Questa news è stata letta 1786 volte.
Pubblicità